Having issues with your ride ? Ask away in here ...
-
subybrumby
- Junior Member
- Posts: 870
- Joined: Thu Jun 28, 2007 5:03 pm
- Location: Toowoomba
Post
by subybrumby » Wed Aug 13, 2008 7:56 pm
Hi guys, I am in the process of exchanging rear half axles in the back of my brumby. The large notched screw that holds the rear bearing needs a special tool. Like this ...its a half inch drive socket
[ATTACH]1209[/ATTACH]
Now this has probably been discussed before, but I've got a bloke gonna try and make something up for me out of pipe. What have others done to get this off...I used a punch on the nut on the donor hubs and found this nut to be very soft and easily damaged.
Any tricks or ideas other than what I'm doing?
Thanx (Trevor)
-
Matatak
- Senior Member
- Posts: 2393
- Joined: Fri May 04, 2007 8:06 pm
- Location: Gnangara next to pines
Post
by Matatak » Wed Aug 13, 2008 8:02 pm
ive used a Punch and hammer before and twisted em undone. not hard unless their seized Lol.

Wagon is no longer....
The Subaru Wacky Workshop -
All About the WA Boys 
-
subybrumby
- Junior Member
- Posts: 870
- Joined: Thu Jun 28, 2007 5:03 pm
- Location: Toowoomba
Post
by subybrumby » Wed Aug 13, 2008 8:29 pm
Yea. I did that on the donor hubs in the vice to get the axles I want out. I just found that the punch was stuffing up the slots on the nut so want to go easier on the ones on my car. Also would prefer to do them on the car so I don't upset the brake lines (Gettin lazy) I might have to wait to see what me mate makes up for me, I think he will come good. he had a little MY wagon but sold it and is pretty handy with this sort of thing. I reckon a suitable sized slotted pipe would do the trick with a hole on the other end to slip a bar through.
-
AlpineRaven
- Senior Member
- Posts: 3682
- Joined: Wed Oct 19, 2005 10:00 am
- Location: Melbourne, Victoria, Australia.
Post
by AlpineRaven » Wed Aug 13, 2008 9:37 pm
Yeah its not hard to make out from a pipe and weld the old socket on it... or use a punch & soft hammer. I've done that before.
Cheers
AP
Subarus that I have/had:
1995 Liberty "Rallye" - 5MT AWD, LSD - *written off 25/8/06 in towing accident.
1996 Liberty Wagon - SkiFX AWD 5MT D/R, Lifted.. Outback Sway Bar, 1.59:1 Low Gearing see thread:
1.59:1 in EJ Box Page
Sold at 385,000kms in July 2011.
2007 Liberty BP Wagon, 2.5i automatic
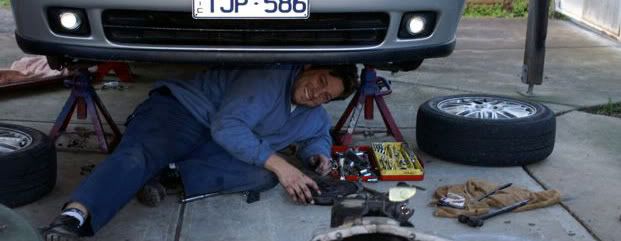
-
brumbyrunner
- General Member
- Posts: 1743
- Joined: Mon Apr 10, 2006 10:00 am
- Location: SEQ
Post
by brumbyrunner » Wed Aug 13, 2008 11:06 pm
You don't have to get so elaborate.
I made a tool from a piece of 40x40RHS with 2 short bits of 50x6 flat bar welded on the side. That way you pick up all 4 contact points at once and nothing gets damadged. Good for servicing bearings all the time.
Settlement Creek Racing
-
rtcb65
- General Member
- Posts: 1354
- Joined: Sun Jul 29, 2007 1:07 pm
- Location: Gympie
-
Contact:
Post
by rtcb65 » Thu Aug 14, 2008 3:19 pm
We got sick of banging away with a drift and hammer so steve made up the remover and also the castle nut spanner.They work well.

rtcb65
------------------
Redneck Rick.
1997 Gen 3 outback. GT forester wheels . Hopefully more changes to come. Proud Supporter And User of -----------C R O S S B R E D --- P E R F O R M A N C E ---- Products
[SIGPIC][/SIGPIC]
-
subybrumby
- Junior Member
- Posts: 870
- Joined: Thu Jun 28, 2007 5:03 pm
- Location: Toowoomba
Post
by subybrumby » Thu Aug 14, 2008 9:46 pm
Thanks for all the input. I had bought a 36ml impact socket for my rattle gun for removing the wheel castle nuts sooo...
Today, I quickly made up a small tool from a piece of pipe (Same pipe that holds road signs from small piece of scrap from work) that is the same dimension as the slotted nut. I cut the nutches out with an angle grinder and then welded a flat washer over the end (from the radius rod of an XD falcon) and then welded a spare castle nut from the donor hub. It came of pretty quickly while the hub was still attached to the car. Yippee (Ignore the welds or I'll get depressed) Just a quick fixit. I might make something more permanent along this line later on. Anyway it worked and achieved what I wanted to do. Its rough as guts but its only a prototype to see if it would work. Thanks to those that replied, they are all good ideas.
[ATTACH]1210[/ATTACH]
[ATTACH]1211[/ATTACH]
-
dommie13
- Junior Member
- Posts: 33
- Joined: Thu Aug 28, 2008 2:43 pm
- Location: Brisbane
Post
by dommie13 » Fri Aug 29, 2008 10:59 am
Hey,
Anyone want to let us know some dimensions of this tool and I can make up a drawing on the computer and cut one out at school with the CNC machine.
Cheers
,Dom.
-
subybrumby
- Junior Member
- Posts: 870
- Joined: Thu Jun 28, 2007 5:03 pm
- Location: Toowoomba
Post
by subybrumby » Fri Aug 29, 2008 4:52 pm
No worries, I'll get dimensions from one of the old locking rings I've got in the shed. I'll put my hand up for one if you are going into business. I'll get it to you tomorrow.
-
dommie13
- Junior Member
- Posts: 33
- Joined: Thu Aug 28, 2008 2:43 pm
- Location: Brisbane
Post
by dommie13 » Fri Aug 29, 2008 6:15 pm
subybrumby wrote:No worries, I'll get dimensions from one of the old locking rings I've got in the shed. I'll put my hand up for one if you are going into business. I'll get it to you tomorrow.
Cheers,
Yea if I get to make em' you can have one for the cost of materials and postage.
,Dom.
-
steptoe
- Master Member
- Posts: 11582
- Joined: Thu Oct 06, 2005 10:00 am
- Location: 14 miles outside Gotham City
Post
by steptoe » Sat Aug 30, 2008 9:26 am
I was thinking the first pic looks like a modified socket of whatever fits
-
dommie13
- Junior Member
- Posts: 33
- Joined: Thu Aug 28, 2008 2:43 pm
- Location: Brisbane
Post
by dommie13 » Sat Aug 30, 2008 12:13 pm
UPDATE: I've designed the tool with the handle and all 4 notches, I have just guesstimated the placement/size of the notches and the size of the head.
I'm just waiting on some measurements.
The Tool with Handle
View from the top
The head on it's own
Cheers
,Dom.
-
subybrumby
- Junior Member
- Posts: 870
- Joined: Thu Jun 28, 2007 5:03 pm
- Location: Toowoomba
Post
by subybrumby » Sat Aug 30, 2008 8:04 pm
I'm just a plodder, not an engineer but here goes"-
[ATTACH]1233[/ATTACH]
[ATTACH]1234[/ATTACH]
[ATTACH]1235[/ATTACH]
[ATTACH]1236[/ATTACH]
and this
[ATTACH]1237[/ATTACH]
-
subybrumby
- Junior Member
- Posts: 870
- Joined: Thu Jun 28, 2007 5:03 pm
- Location: Toowoomba
Post
by subybrumby » Sat Aug 30, 2008 8:10 pm
and this :-
[ATTACH]1238[/ATTACH]
Depth of tool needs to be about 100ml to clear rear of axle (like a plug spanner)
Teeth width 5ml
space between teeth 10ml
Depth of teeth 5ml.
Took these measurements best I can. An oil seal sits inside the ring.
I've got a bloke here in toowoomba who will take one also so send me two if you get it up and running thanks. He'll pay. (someone may want to check those measurements or test on a locking ring if you can get your hands on one.)
T
-
dirty skirt
- Junior Member
- Posts: 71
- Joined: Mon Jan 30, 2006 10:00 am
- Location: nundle nsw
Post
by dirty skirt » Wed Sep 03, 2008 5:52 pm
hey guys would it be better to have on the end with out the lugs a flat piece of plate with a nut on it so you could use a torque wrench to do the nut up or are they done up F T
cheers steve
-
dommie13
- Junior Member
- Posts: 33
- Joined: Thu Aug 28, 2008 2:43 pm
- Location: Brisbane
Post
by dommie13 » Wed Sep 03, 2008 6:01 pm
dirty skirt wrote:hey guys would it be better to have on the end with out the lugs a flat piece of plate with a nut on it so you could use a torque wrench to do the nut up or are they done up F T
cheers steve
Well the design I have at the moment has a 1/2 inch socket drive in it but Tech teacher says that will be too hard to make so it's gonna have a handle, but now you bring this up I spose we could weld a nut on the end so you can use a torque wrench.
Will consider it.
,Dom.
-
subybrumby
- Junior Member
- Posts: 870
- Joined: Thu Jun 28, 2007 5:03 pm
- Location: Toowoomba
Post
by subybrumby » Wed Sep 03, 2008 7:02 pm
Dom, I posted that lock nut to you today. Dirty Skirts post has some merrit.
If you want to unscrew this thing on the vehicle without taking the trailing arm off, it could be a bit restricted getting access to the area to get some grunt on it. Maybe two holes through the end at 90 degrees to each other to slide a pinch bar through or something like that. Or the 'weld a nut idea". I would go for the 36ml castle nut because most have a socket for it and rattle gun and torque wrench etc.
My first pathetic design was based on that idea so I could grab it in a number of ways...it worked until my cheap sh....tty pipe I built it from disintegrated.
When you get the locking ring, you'll see that it can be easily damaged. We need to get a good firm grab of it without slippage. Also the factory tool has a lip on each tooth (See previous photos) so it recessess into the ring and locks on..
Cheers T
-
dommie13
- Junior Member
- Posts: 33
- Joined: Thu Aug 28, 2008 2:43 pm
- Location: Brisbane
Post
by dommie13 » Thu Sep 04, 2008 3:43 pm
subybrumby wrote:Dom, I posted that lock nut to you today. Dirty Skirts post has some merrit.
If you want to unscrew this thing on the vehicle without taking the trailing arm off, it could be a bit restricted getting access to the area to get some grunt on it. Maybe two holes through the end at 90 degrees to each other to slide a pinch bar through or something like that. Or the 'weld a nut idea". I would go for the 36ml castle nut because most have a socket for it and rattle gun and torque wrench etc.
My first pathetic design was based on that idea so I could grab it in a number of ways...it worked until my cheap sh....tty pipe I built it from disintegrated.
When you get the locking ring, you'll see that it can be easily damaged. We need to get a good firm grab of it without slippage. Also the factory tool has a lip on each tooth (See previous photos) so it recessess into the ring and locks on..
Cheers T
Yep got it today, Did up some drawings, I didn't bother putting the nut on the end of the drawing as we'll just weld it on.
I'll try and get something happening with the tech teacher, I let ya know.
,Dom.
-
subybrumby
- Junior Member
- Posts: 870
- Joined: Thu Jun 28, 2007 5:03 pm
- Location: Toowoomba
Post
by subybrumby » Thu Sep 04, 2008 7:42 pm
Great...that looks more to the size...looking good.